OK , let me start by saying I have no idea what I'm doing

So far this is what I have done , the rest may take a week or so to be finished .
First I drew a knife on some paper and cut it out . Then I traced the pattern onto my Circular Saw blade .

Now I get ready to cut it out with my quality angle grinder from Supacheap Auto , cost me a whole $17


Here it is halfway through .Make sure you always wear eye protection , no good if ya can't see what ya doing


Here is the blank cut out .

Now I tidy it up a bit on my bench grinder

Drill some holes in the handle for the pins that will hold the scales on

And here we have the blank ready for the next stage of more grinding of the edge etc

As I said , I am no expert , so any suggestions much appreciated


Oky doky ,, no buildalong would be complete without mistakes , so you learn what NOT to do

I bought a Disc attatchment for my drill to put the Bevel on the blade ,,a Linisher would be better .
Here I am starting to grind it

I cant seem to get both angles consistent , it may just be practise , but as I said , a linisher may be better , as thats what I have read .
Here are some pics of the angles/mess and I also polished some of the marks out of the blade ,, you will see whats left of the mark . Maybe I can fix the Bevel with a file , we will see later .



When it comes down to it ,, I suppose it is only cosmetic , but I want it to be perfect ,, maybe a big ask first time around .
See ya again soon

Well I bought a bloody big Mill file today and tidied up the bevel . Not perfect but a lot better



Todays update .
I heat treated the knife by dragging out the little Weber . Must get a blow torch



I heated the steel up to a point where a Magnet wouldn't stick.
Then I quenched it in a bucket of old cooking oil.

After this I ran a file across it to see if the file would dig in , well it did , so I repeated the process a second time and the file skated across the blade without digging as much

From there it went into the oven set on 200 C for 45 minutes to anneal the blade IE to take out some of the brittleness .
This is what it looks like after the process

And this is what it is looking like after a little bit of a clean up with some 180 grit sandpaper .
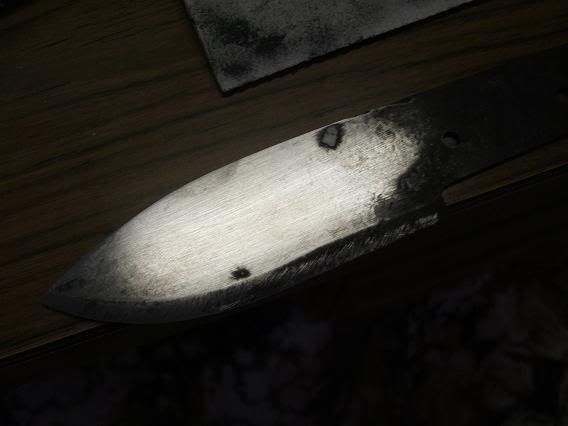
I will clean it up more later , not sure if I'll take it so far as a Mirror finish though .
All thats need then is to put a handle on it . More to come on that later .

DAMN ,, I just noticed I forgot to drill some more holes for the epoxy to go into on the handle !! Oh well I'm sure it will be right
